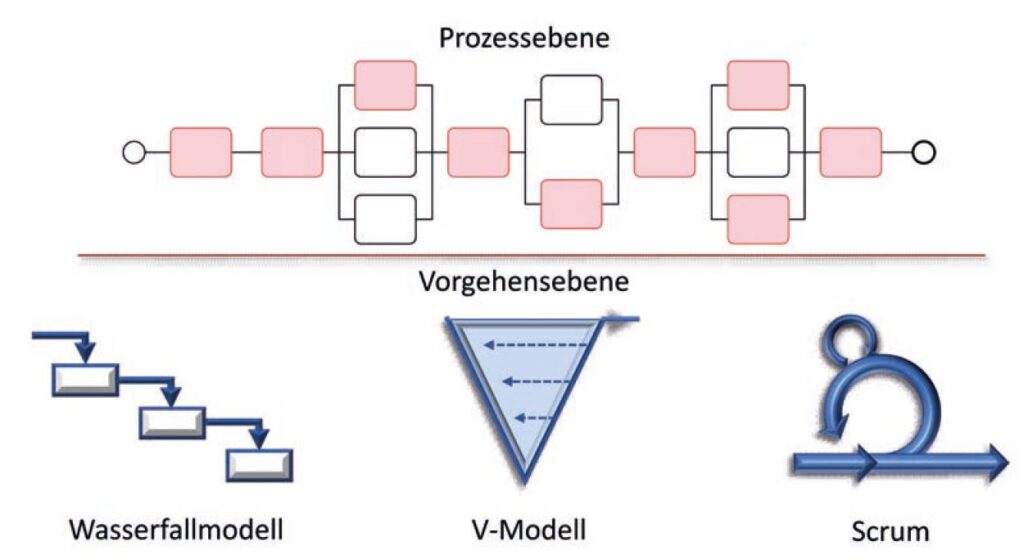
Die Automobilindustrie hat in den letzten Jahrzehnten die Entwicklung mechanischer Bauteile professionalisiert. Dabei kam der Kommunikation mit den Lieferanten eine besondere Bedeutung zu. Die verschiedenen Abstimmungsprozesse erfolgten z.B. an gemeinsamen Quality Gates.
In der Zwischenzeit dominieren allerdings nicht mehr nur die mechanischen Bauteile, sondern es zieht immer mehr Software in das Auto ein. Dabei sind die Entwicklungszyklen von mechanischen Bauteilen und Software-Komponenten sehr unterschiedlich. Wie wir alle wissen, liegt der Technologiezyklus z.B. für ein Smartphone in der Zwischenzeit weit unter einem Jahr. Ähnlich sieht es bei anderen digitalen Angeboten aus. Bei komplexen mechanischen Bauteilen eines Autos sind die Zyklen allerdings wesentlich länger.
Es besteht somit ein Bedarf an Abstimmungsprozessen nicht nur zwischen dem Hersteller (OEM) und seinen wichtigsten Modul- und Systemlieferanten (Tier 1), sondern auch innerhalb der jeweiligen Projektebenen. Es erweist sich in diesem Zusammenhang als hilfreich, eine Prozessebene mit den bekannten Phasen und Meilensteinen, und eine Vorgehensebene zu unterscheiden (Abbildung). Hier kommen dann die im Projektmanagement bekannten plangetriebenen, auch die agilen und hybriden Vorgehensmodelle hinzu.
“Es existiert also der Wunsch agile und hybride Methoden im automobilen Produktentstehungsprozess anzuwenden. Auch wurden bereits erste Versuche hierzu durchgeführt, die deren positiven Effekt festgestellt haben. Was bisher aber noch fehlt, ist ein Leitfaden, der Unternehmen bei der Einführung dieser Vorgehensmodelle unterstützt und die verschiedenen Möglichkeiten zur Kommunikation mit Partnern in vorhergehenden bzw. nachfolgenden Tiers aufzeigt” ( Schmidtner, M.; Timinger, H. (2020): Automatisiertes Tailoring von Produktentstehungsprozessen, in: ProjektmanagementAktuell 02/2020).
In einem geförderten Projekt wird so ein Leitfaden entwickelt. Die Autoren haben weiterhin in einem Paper zusammengefasst, wie so ein adaptives System in der Automobilindustrie aussehen kann: Schmidtner, Markus; Timinger, Holger (2021): HyValue – Ein adaptives Referenzmodell für dem hybridem Produktentstehungsprozess in der Automobilindustrie. In: Lehmann, Lisa; Engelhardt, Doris; Wilke, Winfried (Hrsg.): Kompetenzen für die digitale Transformation 2020. Berlin: Springer Vieweg, S. 37-48.

Solche Zusammenhänge thematisieren wir auch in den von uns entwickelten Blended Learning Lehrgängen, Projektmanager/in (IHK) und Projektmanager/in Agil (IHK), die wir an verschiedenen Standorten anbieten. Weitere Informationen zu den Lehrgängen und zu Terminen finden Sie auf unserer Lernplattform.